
- About Us
-
For Individuals
-
Career Exploration »
- Vocational Rehabilitation
- Veteran Services
- Youth Services
- Young Adult Exploration
- Young Adult Financial Aid
- Young Adult Service Elements
- Adult Education & Literacy
- When I grow Up Curriculum
- Your Career Your Choice
- Senior Community Service Employment Program (SCSEP)
- Early Childcare Expansion
- Early Education Quality
- Early Education Quality »
- Financial Aid »
-
Career Exploration »
- For Employers
- Find a Career Office
-
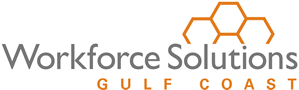
OJT for the Production Industry: Building a Better Future
Labor shortages in the manufacturing industry reached a high of 780,000 unfilled jobs in late 2022, and production workers were at the top of that staffing challenge. Production jobs require a high level of technical skill and employment candidates usually don’t have the training or experience to handle these positions. That’s where on the job training (OJT) comes in. OJT programs provide hands-on skills and experience to help new hires succeed in production environments. OJT provides a number of benefits to employees and employers, including partial wage reimbursement and employee coaching. Here are a few reasons to start OJT at your company.
Specialized Skill Development
The production industry demands specialized technical skills that are unique to each role. Whether it’s mastering complex machinery, understanding chemical processes, or performing intricate welding, OJT programs are targeted to directly align with a new hire’s role. Workforce Solutions OJT consultants can build on your existing training or create a new program to make sure your new hires get the exact skills needed for their roles.
Hands-on Training
There’s no substitute for real-world experience, and OJT provides a way for new hires to learn by doing. They’re integrated into existing teams, so they work alongside seasoned workers from day one. This practical, hands-on approach accelerates their skill development and helps them learn proper, safe operational techniques from experienced employees.
Improved Safety
Safety is the top priority in production, and hands-on training reinforces the importance of following safety protocols. New hires aren’t watching videos or reading handouts, they can see and feel, in real time, the importance of safety standards. OJT fosters a culture of safety and responsibility among teammates.
Training Flexibility
The production industry encompasses many sectors, from manufacturing to petrochemicals. OJT programs offer the flexibility to create custom, scalable training programs that meet the unique requirements of each role. These programs can be scaled up or down depending on the number of new hires brought onboard at once.
Reduced Downtime
Can you afford to send new hires offsite for weeks of training? OJT minimizes downtime by having new hires function as part of the team while they’re still in training. OJT programs are seamlessly integrated into the workday to keep production rolling while new hires are learning.
New Hire Retention
Workforce Solutions provides 90 days of employee coaching through the OJT program. There is a formal 30-, 60-, and 90-day check-in with new hires, and coaches are available any time the new hire needs help navigating their new environment. Employers can also take advantage of coaching to help reinforce training or provide additional feedback on skill development. Coaching keeps new hires engaged and supports them as they learn, so they’re more likely to excel and stay with the company.
Manufacturers, chemical plants, refineries, and other production facilities are in the middle of a technological revolution with automation and AI technologies. It’s going to take a highly skilled workforce to navigate these changes, and companies need a strategy to close the current skills gap. OJT can bridge that gap with customized training and support.
Workforce Solutions assists with OJT development, candidate search and placement, and a lot more. Email talent@wrksolutions.com or call 713-688-6890 to get started!
